ACRYLIC
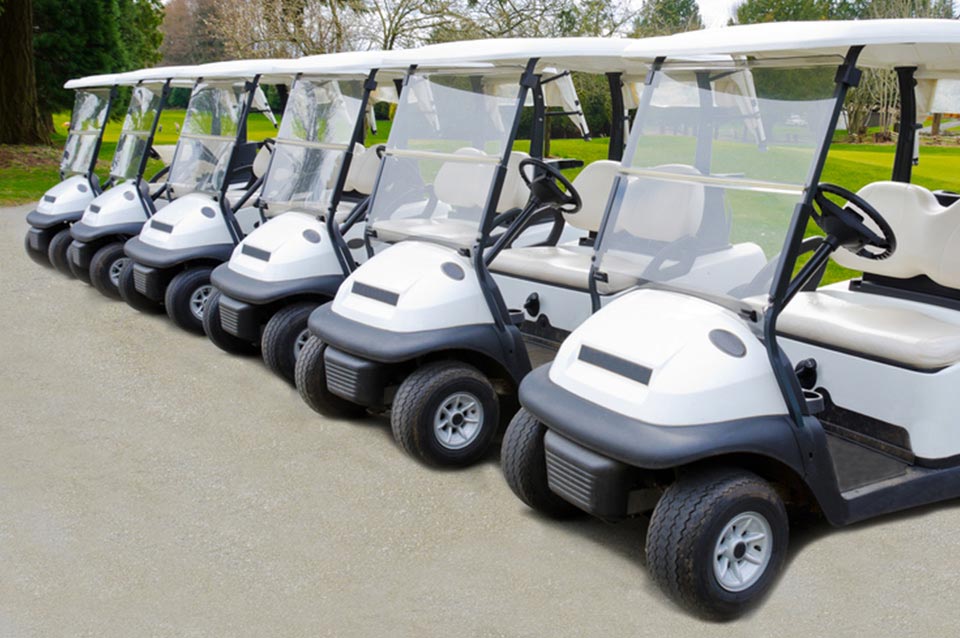
.jpg?sfvrsn=f9d3df4f_4)
.jpg?sfvrsn=e534c9c2_4)
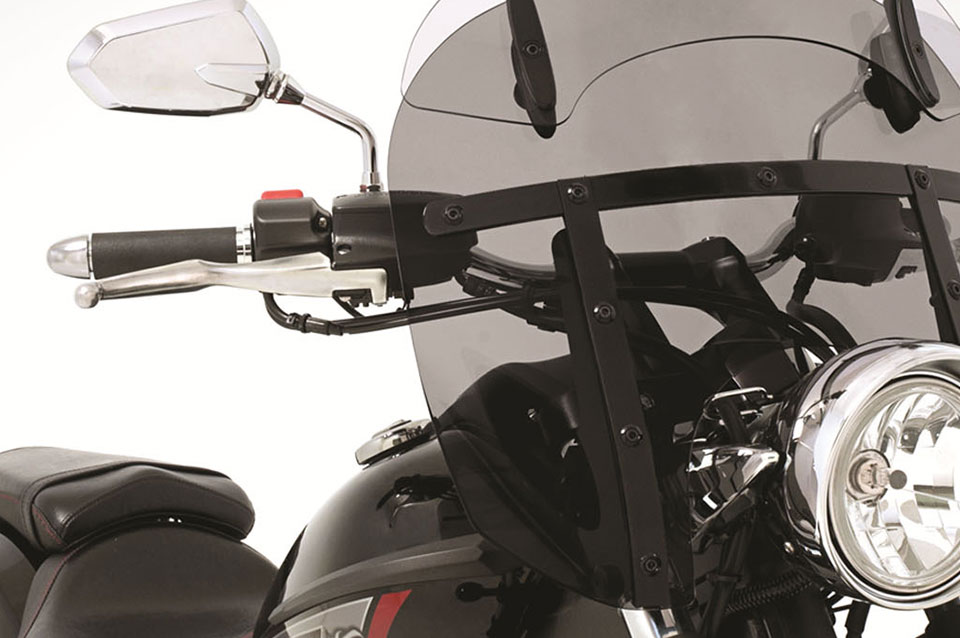
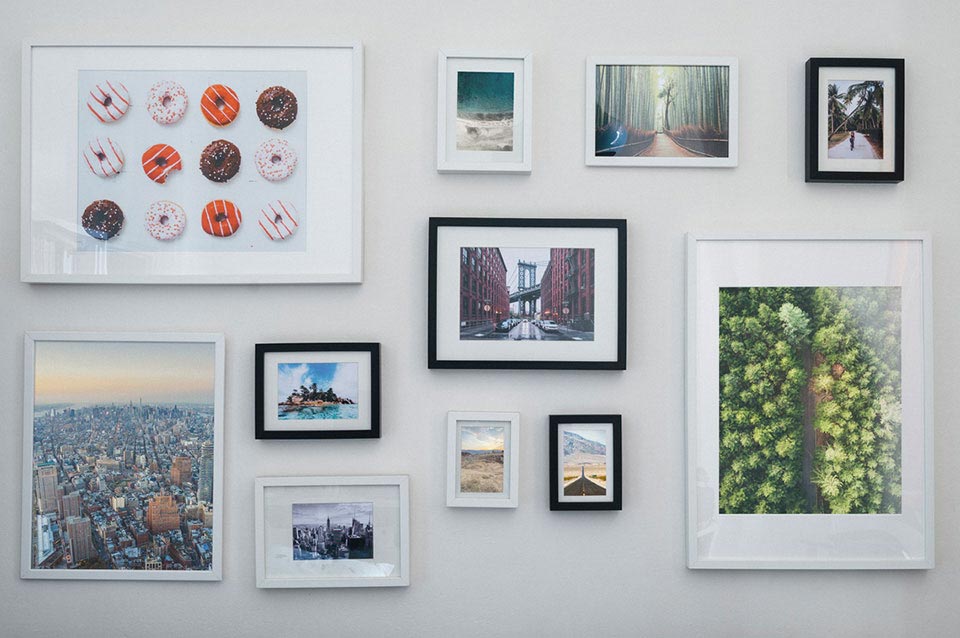
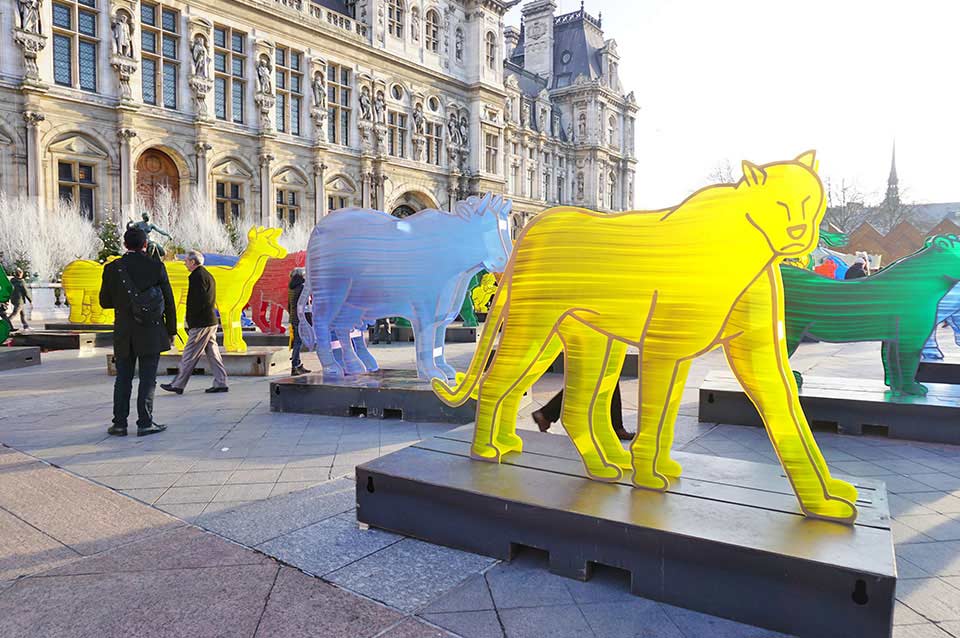
PMMA
Impact and weather resistant, crystal clear or colored, Acrylic sheet, also called PMMA is a versatile, general-purpose thermoplastic sheet. Ideal for automotive and transportation and almost any application, acrylic sheet boasts a high molecular weight that enables superior fabrication and forming. It’s the industry choice for point-of-purchase displays, lighting and furniture.
STRENGTH
Three times stronger than window glass
FABRICATION READY
Ideal for almost any type of glazing or signage
CRYSTAL CLEAR
UV stabilization protects the sheet from yellowing
DURABILITY
Impact and weather resistant
Search Our Catalog