MOLD DESIGN AND CONSTRUCTION
Over 40 years in optical-grade mold design
Solving complex challenges globally
State-of-the-art design for distortion-free optics
Pre-production analysis prevents costly issues
OUR MOLD DESIGN PROCESS
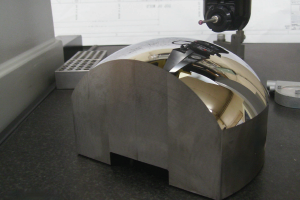
Our Mold Services:
• Mold design and application consulting
• Part design assistance
• Lens and optical design analysis for manufacturing
• Reverse engineering
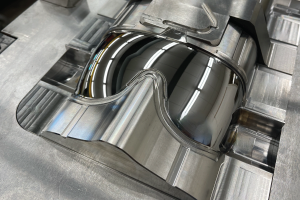
Materials for Crafting Molds:
• 420 Stainless steel
• Aluminum
• Aluminum bronze
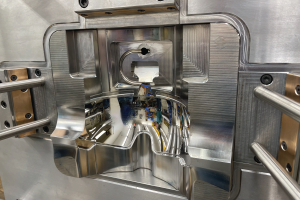
Available Coating Options:
• Nickel
• Chrome
• Titanium
FREQUENTLY ASKED QUESTIONS - TOOLING
How large of a part can you make an optical mold for?
Regularly PLASKOLITE builds molds for full-face protection products.
Does PLASKOLITE build any non-optical molds?
PLASKOLITE builds molds for MIM, multi-material, and conventional parts. Typically, these molds have a greater level of complexity.
How small of a part can you make an optical mold for?
PLASKOLITE has built molds for parts as small as cell phone camera lenses.
What makes an optical mold different from a non-optical mold?
Optical molds require specialized attention to surface geometry and form, surface finish, and optical alignment.
What is diamond turning?
Diamond turning is a process by which a non-ferrous material is machined at the nano level to achieve superior surface finishes on geometries that may be non-conventional.
FREQUENTLY ASKED QUESTIONS - OPTICAL
What is an optical design correction?
To meet the demanding standards set by many industries, the finished optical part must have its optical surfaces adjusted to achieve optimal performance.
What geometric shapes do you work with?
Flats, spheres, cylinders, conics, torics, aspheres…
How do you specify the surface finish of your molds for optical parts?
Optical finishes are called out in many ways; typically, we refer to “scratch/dig” specifications and steel roughness in Ra or Angstroms. At PLASKOLITE, we typically achieve finishes in the range of less than 100 Angstrom or possibly better.